Bending and Forming
Interested in learning more about whether press brake bending and forming is the right process for your project? Our team is ready to help. Contact us today or submit a quote and we'll get back to you right away.
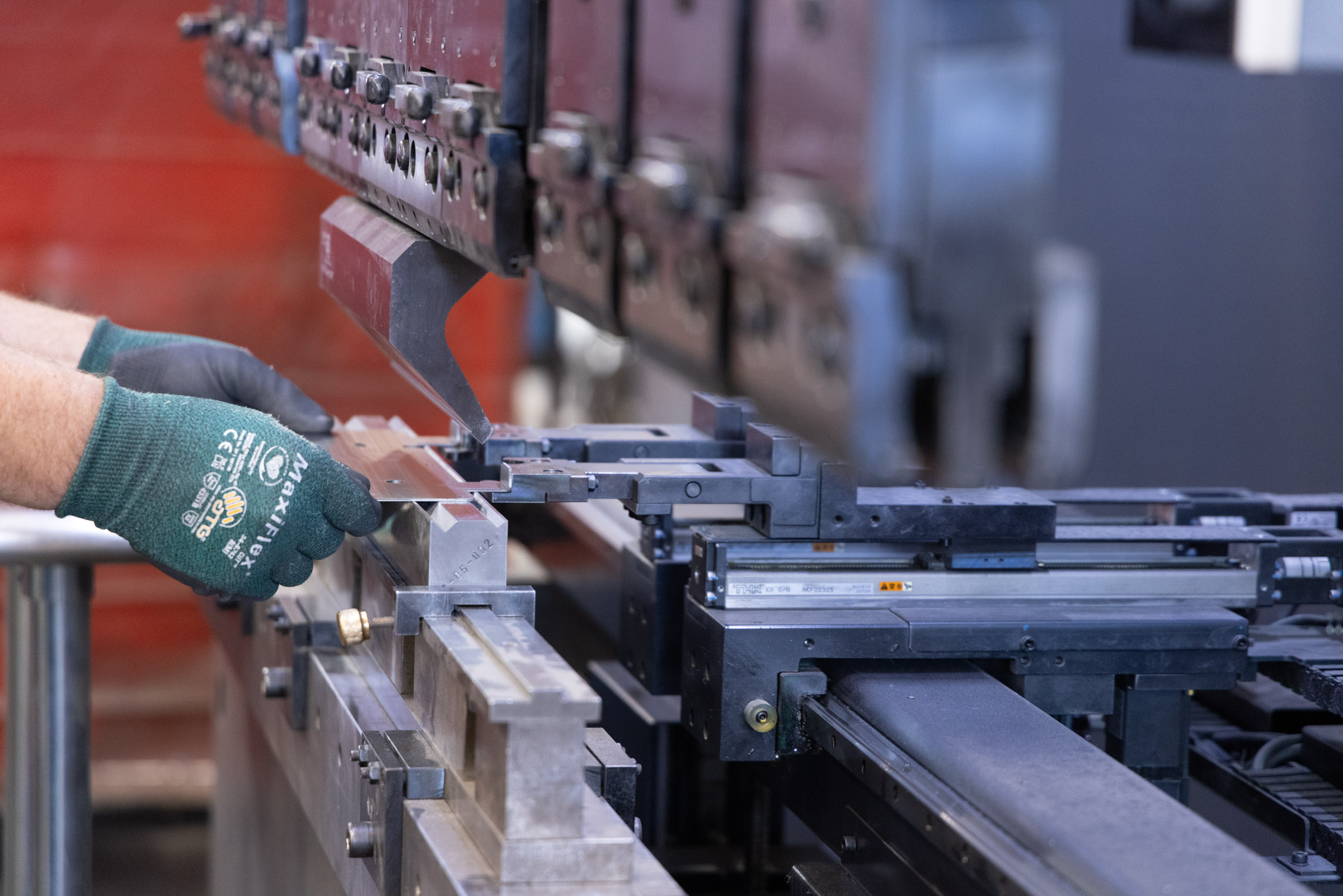
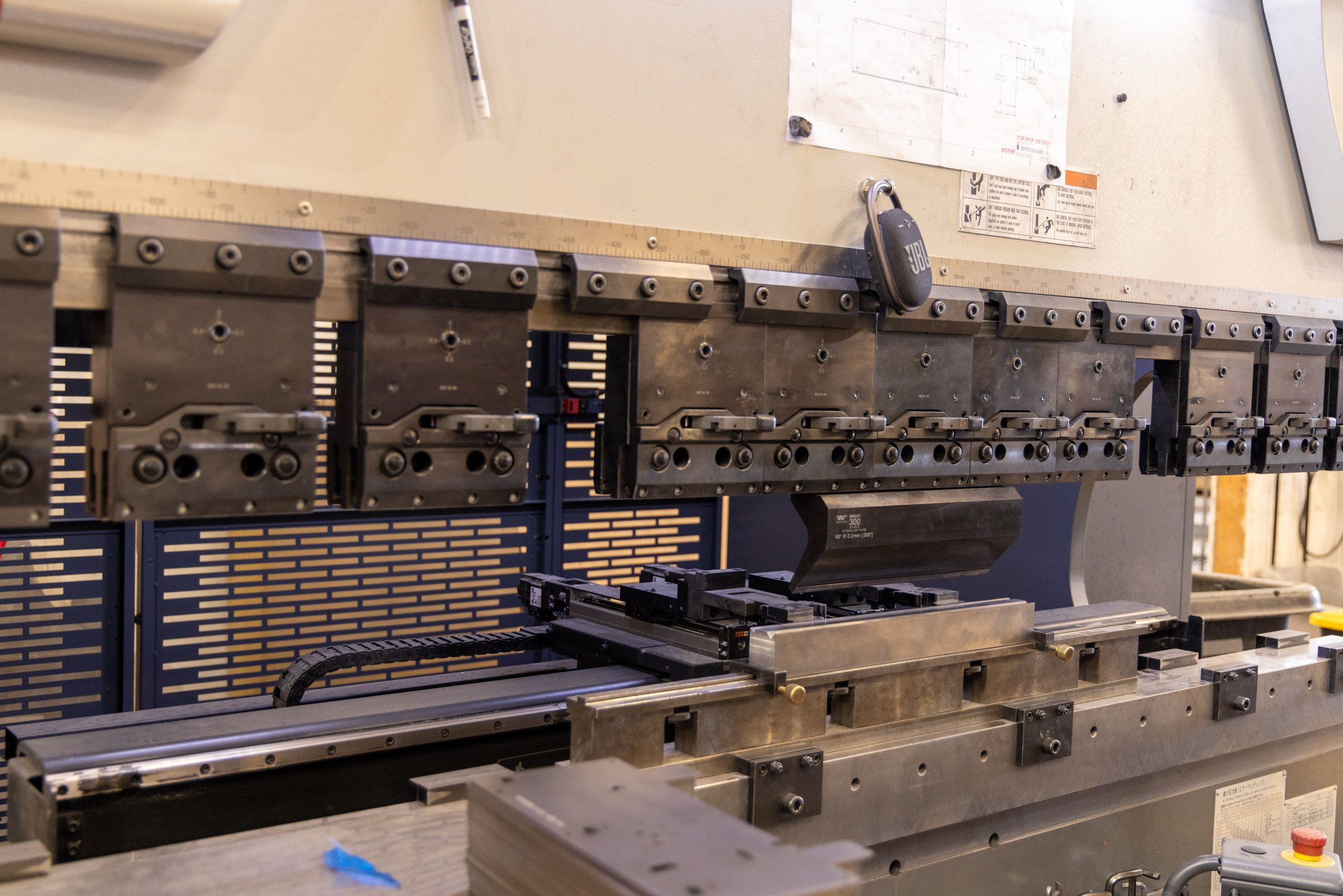
Our Bends Are Unparalleled
At Ferreus, our expertise in sheet metal bending sets us apart as a leader in precision manufacturing. We employ advanced bending machines and skilled technicians to ensure that every bend meets exact specifications with unparalleled accuracy and consistency. Whether it's simple bends or complex geometries, our capabilities allow us to handle a wide range of materials and thicknesses, delivering superior quality and reliability. Our commitment to precision bending is evident in every project, ensuring that each component meets stringent quality standards and fulfills the unique requirements of our clients.
Precision Bending
Our state-of-the-art bending machines ensure precise and consistent bends, meeting exact specifications for every part.
.png)
Capability to produce complex bends
Ferreus excels in producing both simple bends and complex geometries with precision, leveraging advanced techniques and skilled craftsmanship to meet diverse project requirements.
Skilled technicians
Our experienced team handles various materials and thicknesses with expertise, ensuring accuracy and efficiency in all bending processes.